Thermoforming and FST Requirements: Revolutionizing Material Selection in Rail and Bus Industries
In the ever-evolving landscape of material science and manufacturing, thermoforming has emerged as a pivotal technique, especially in industries like rail and bus transportation. A crucial aspect that governs material selection in these sectors is adherence to Flame, Smoke, and Toxicity (FST) requirements.
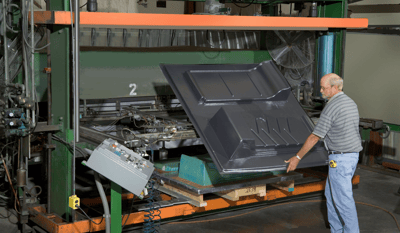
Understanding Thermoforming
Thermoforming is a manufacturing process where a plastic sheet is heated to a pliable forming temperature, formed to a specific shape in a mold, and trimmed to create a usable product. This technique is favored for its cost-effectiveness, versatility, and efficiency in producing large parts with intricate designs.
The Significance of FST Requirements
FST requirements are a set of standards that assess materials for their flame retardancy, smoke emission levels, and toxicity when exposed to fire. In the context of public transportation like buses and trains, materials used must meet these requirements to minimize the risk of fire, reduce the danger from smoke inhalation, and prevent toxic fumes, ensuring passenger safety.
The Federal Transit Administration (FTA) and the Federal Rail Administration (FRA) set forth rigorous requirements that are designed to assess the safety of materials used in transportation. These standards are not just formalities; they are essential in mitigating risks associated with smoke emission and flammability - two factors that can significantly impact passenger safety in the event of an emergency.
Key among these standards are the ASTM E-662 and ASTM E-162 tests. ASTM E-662 measures the smoke density produced by materials, a crucial factor in visibility during a fire, which can be the difference between safety and catastrophe. On the other hand, ASTM E-162 focuses on the surface flammability of materials. This test helps in understanding how quickly a fire can spread, allowing manufacturers and operators to choose materials that offer greater resistance to fire.
Incorporating these standards into the design and selection of materials is not just about ticking a box in the compliance checklist. It is about a commitment to passenger safety, ensuring that every component used in transit and rail systems can withstand extreme conditions and not exacerbate a dangerous situation.
As we move towards more advanced and faster modes of transportation, the adherence to these FTA and FRA requirements becomes even more crucial. They serve as a benchmark for safety, guiding manufacturers and operators in making informed decisions that prioritize the well-being of passengers and the integrity of our transportation systems.
While the technical aspects of ASTM E-662 and E-162 may seem complex, their importance cannot be overstated. They are the unsung heroes in our journey towards safer, more reliable transportation. By understanding and adhering to these standards, we take a significant step forward in protecting lives and enhancing the quality of our transit and rail systems.
Materials That Meet FST Standards
Several materials have been developed to comply with FST standards without compromising on functionality or aesthetics:
1. High-Performance Thermoplastics: Materials using blends of Polycarbonate and proprietary additives can be engineered to be flame retardant while maintaining their mechanical properties.
2. Thermoset Composites: These are often used in rail and bus interiors. They can be formulated with additives to improve their flame retardancy and reduce smoke and toxic emissions.
3. Advanced Foam Cores: Foam cores used in composite panels offer excellent fire resistance while providing thermal insulation and noise reduction, crucial for passenger comfort and safety.
4. Specialty Coatings: Applying flame-retardant coatings to materials can significantly enhance their FST properties. These coatings are particularly useful in retrofitting existing materials.
Kydex 2200LT and 2210LT are specially formulated to comply with the rigorous safety standards set by the FTA and FRA. Kydex 2200LT and 2210LT are renowned for their low smoke production and minimal flame spread, aligning perfectly with the ASTM E-662 and ASTM E-162 standards.
Their use in transportation systems exemplifies an active commitment to safety, ensuring that every component, down to the materials used, contributes to the overall security and efficiency of transit and rail systems. The incorporation of Kydex 2200LT and 2210LT serves as a benchmark for material selection, embodying the highest standards of safety and reliability essential in modern transportation.
Challenges and Innovations
One of the challenges in developing materials that meet FST standards is balancing safety with other performance requirements like durability, weight, and cost. Innovations in this area include the development of nano-composites and hybrid materials that offer enhanced fire resistance without compromising other essential properties.
Impact on the Rail and Bus Industries
Materials that meet FST requirements have a profound impact on the rail and bus industries. They allow manufacturers to design safer vehicles without significantly increasing production costs or altering manufacturing processes. Moreover, these materials can lead to lighter, more energy-efficient vehicles, aligning with the global push toward sustainability.
The integration of thermoforming with FST-compliant materials represents a significant leap forward in the transportation industry. It ensures that safety remains paramount without hindering design flexibility or cost-effectiveness. As material science continues to advance, we can expect to see even more innovative solutions that will further enhance passenger safety and comfort in public transportation.