HVAC
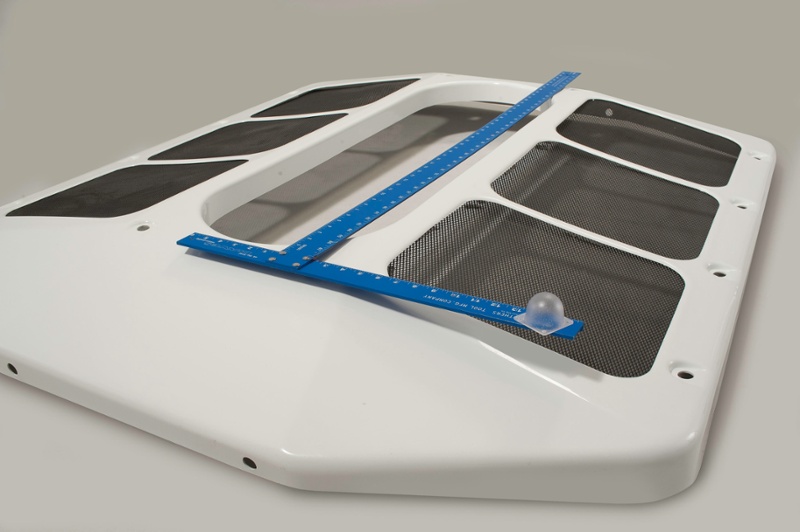
Heating, Ventilation, and Air Conditioning (HVAC) manufacturers constantly seek innovative methods to improve efficiency, reduce costs, and enhance product performance.
One such method gaining significant traction is thermoforming. This versatile manufacturing process involves heating a plastic sheet to a pliable forming temperature, shaping it to a specific form in a mold, and trimming it to create a usable product.
Thermoforming has improved the production of various HVAC components, offering a perfect blend of design flexibility, cost-effectiveness, and durability.
Benefits of Thermoforming in HVAC
Cost-Effective Production
Thermoforming offers a cost-efficient method for producing HVAC components, especially for medium to large production runs.
Design Flexibility
Complex shapes and contours can be easily achieved, allowing for innovative designs in HVAC systems.
Lightweight Components
Thermoformed parts are typically lighter than those made with traditional methods, contributing to overall system efficiency.
Durability
When appropriate materials are used, thermoformed components can withstand harsh environments and temperature fluctuations common in HVAC applications.
Rapid Prototyping
Thermoforming enables quick production of prototypes, accelerating the development and testing of new HVAC designs.
Consistency
The process ensures high repeatability, maintaining consistent quality across large production runs.
Applications in HVAC
Thermoforming is used to create various components in HVAC systems, including:
Air Ducts: Custom-shaped air ducts that optimize airflow and fit into tight spaces.
Diffusers and Vents: Aesthetically pleasing and functionally efficient air distribution components.
Equipment Housings: Durable and lightweight casings for indoor and outdoor HVAC units.
Control Panel Covers: Ergonomic and visually appealing interfaces for HVAC control systems.
Drainage Trays: Corrosion-resistant trays collect and direct condensate in air conditioning units.
Filter Housings: Custom-designed housings that ensure proper filtration and easy maintenance.
Materials Used in HVAC Thermoforming
The choice of material is crucial in HVAC applications, and several types of plastics are commonly used in thermoforming for this industry. ABS (Acrylonitrile Butadiene Styrene) is a popular choice due to its good impact resistance and dimensional stability, making it ideal for interior components. HIPS (High-impact polystyrene) is often preferred for ductwork and vents as it balances strength and cost-effectiveness.
PC (polycarbonate) is frequently used for outdoor components or parts that need to withstand high temperatures. Its high impact strength and heat resistance make it suitable for demanding environments. For applications requiring clarity, such as sight glasses and display covers, PETG (Polyethylene Terephthalate Glycol) is an excellent option due to its transparency and chemical resistance.
In areas where moisture and chemical exposure are concerns, PP (Polypropylene) is the material of choice. Its resistance to chemicals and moisture makes it ideal for components exposed to condensation or cleaning agents. TPO (Thermoplastic Polyolefin) is often selected for its excellent weather resistance for outdoor HVAC units that must withstand various weather conditions.
Safety is paramount in HVAC systems, so fire-retardant plastics are also commonly used. These specially formulated materials meet fire safety standards crucial for HVAC applications, providing extra protection in emergencies.
The selection of these materials allows HVAC manufacturers to create functional, efficient, durable, and safe components.
By matching the material properties to the specific requirements of each component, thermoforming enables the production of HVAC parts that can withstand the diverse challenges of heating, ventilation, and air conditioning systems while maintaining cost-effectiveness and design flexibility.