Point-of-Purchase (POP) Displays
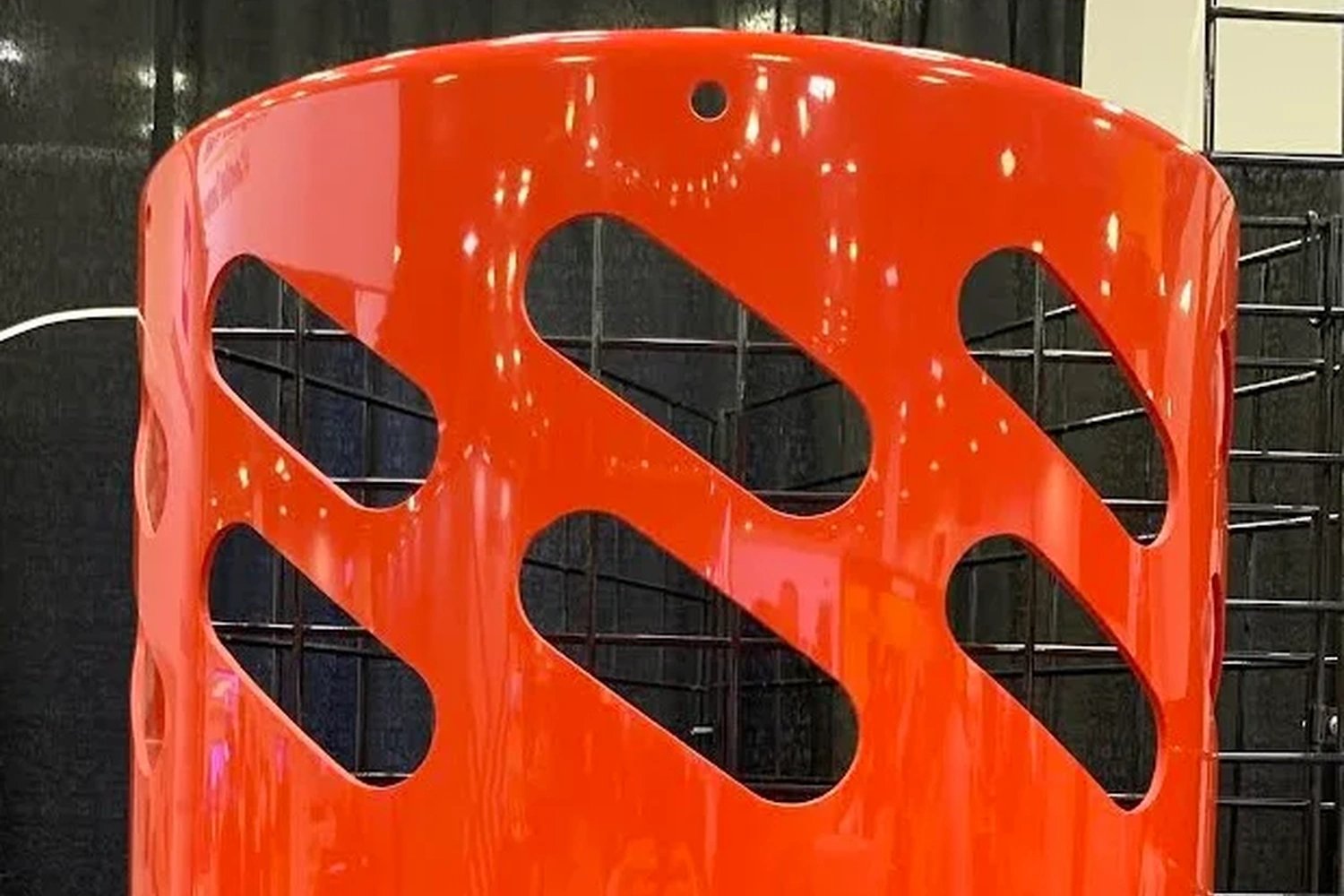
In the dynamic world of retail marketing, point-of-purchase (POP) displays play a crucial role in catching consumers' attention and driving sales.
As brands and retailers seek innovative ways to stand out in crowded marketplaces, thermoforming has emerged as a game-changing manufacturing process for creating eye-catching, durable, and cost-effective POP displays.
Thermoforming offers unparalleled design flexibility, allowing for the creation of complex shapes and textures that can make your product displays truly pop.
Benefits of Thermoforming for POP Displays
Thermoforming offers many advantages for creating point-of-purchase displays. One of the most significant is the remarkable design flexibility it provides. This process allows for creation of complex shapes, curves, and textures, enabling unique and attention-grabbing display designs that can set your products apart from the competition.
Cost-effectiveness is another key advantage, particularly for medium to large production runs. Compared to other manufacturing methods, thermoforming often proves to be a more economical solution, allowing businesses to create impressive displays without breaking the bank.
The resulting displays are typically lightweight yet durable, striking an ideal balance between ease of shipping and installation and long-term resilience in busy retail environments. This characteristic reduces transportation costs and makes it easier for retailers to set up and rearrange displays as needed.
Thermoforming also excels in producing high-quality finishes. The process can create displays with smooth surfaces and sharp details, enhancing the perceived value of the showcased products. This level of quality can significantly impact consumer perception and, ultimately, purchasing decisions.
Another significant advantage is the rapid prototyping and production capabilities of thermoforming. This process enables quick turnaround times for prototypes and final products, allowing for faster market entry and easy design iterations. This agility can be a crucial competitive advantage in the fast-paced retail world.
Lastly, thermoforming offers excellent customization options. The process allows for easy integration of logos, text, and other branding elements directly into the mold, creating seamless and professional-looking displays that reinforce brand identity at the point of purchase.
Applications in POP Displays
The versatility of thermoforming lends itself to a wide array of applications in point-of-purchase displays. Custom-shaped product trays and holders are among the most common applications, providing secure and attractive showcases for specific items. These can be designed to perfectly cradle products, ensuring they're presented in the most appealing way possible while keeping them safe from damage.
Display stands, both freestanding and countertop varieties, are another popular application. These can be crafted to draw attention to specific products or promotions, creating focal points within a retail space. The ability to create complex shapes allows for stands that are functional and contribute to the location's overall aesthetic.
Signage and header cards benefit greatly from thermoforming techniques. Eye-catching, three-dimensional signage can include embossed logos or text, adding depth and interest that flat signs simply can't match. This can be particularly effective for brand reinforcement and promotional messaging.
In our increasingly digital world, thermoformed housings for interactive kiosks are becoming more prevalent. These durable enclosures can be designed to hold digital displays or touchscreens, creating engaging customer experiences while protecting valuable technology.
For larger product lines or promotional campaigns, floor displays created through thermoforming offer an excellent solution. These large-scale, often multi-tiered displays can be designed to hold and showcase multiple products, creating an impactful brand presence in high-traffic areas.
Materials Used in POP Display Thermoforming
The choice of material is crucial in creating practical and durable POP displays. Several types of plastics are commonly used in thermoforming for this industry, each offering unique properties suited to different display needs.
PETG (Polyethylene Terephthalate Glycol) is a popular choice due to its excellent clarity, impact resistance, and ease of fabrication. It's ideal for creating transparent or translucent displays that make products visible. This material is particularly effective for showcasing items where visual appeal is a crucial selling point.
ABS (Acrylonitrile Butadiene Styrene) is often used for displays that require more rigidity and durability. It offers good impact resistance and can be easily painted or printed on, making it perfect for branded displays that need to withstand frequent customer interaction.
HIPS (High Impact Polystyrene) is frequently chosen when a high-gloss finish is desired. It's cost-effective and can be easily thermoformed into complex shapes, making it suitable for various display applications. HIPS is particularly useful for creating eye-catching displays that must maintain their appearance over time.
For outdoor or semi-outdoor displays that need to withstand various weather conditions, Acrylic or PC (Polycarbonate) might be preferred due to their UV resistance and durability. These materials ensure that displays maintain their appearance and structural integrity even when exposed to sunlight or temperature fluctuations.
In cases where a soft-touch or flexible component is needed, TPO (Thermoplastic Polyolefin) or TPE (Thermoplastic Elastomer) can be used. These materials provide a pleasant tactile experience and can be used for grip areas or flexible display parts, adding an extra dimension to customer interaction.
Safety is always a concern in retail environments, and for displays that need to meet specific safety standards, flame-retardant grades of various plastics are available. These materials ensure that the displays comply with retail safety regulations while maintaining their attractive appearance.
The selection of these materials allows POP display manufacturers to create components that are not only visually appealing and functional but also durable and safe. By matching the material properties to the specific requirements of each display, thermoforming enables the production of POP displays that can withstand the rigors of retail environments while effectively showcasing products and enhancing the shopping experience.